Sustainix is dedicated to placing career development at the forefront, enhancing transparency, and offering flexibility and options for advancing careers. Through mutual investment, we can unleash unmatched potential and collaboratively shape a brighter future together.
View Current Openings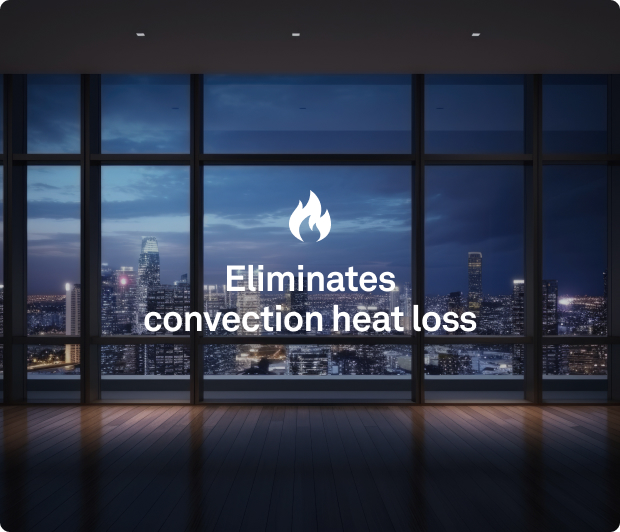
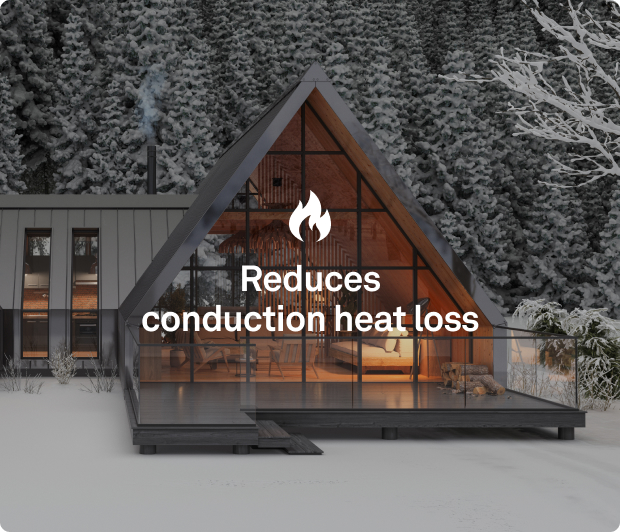
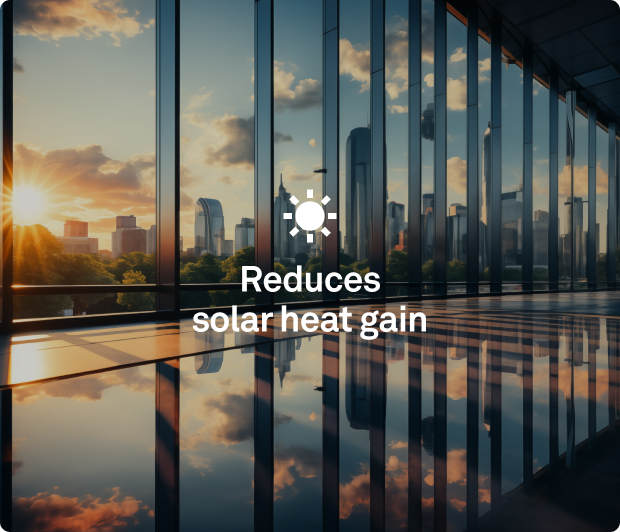
Saving the Planet Just Might be Your Destiny
Here, you’ll work hands-on with a first-to-market product in the industry – a patented new vacuum insulating glass technology that acts as transparent insulation for buildings. Our technological advancements in glass will accelerate us to net zero for buildings. And with mass adoption, Sustainix glass can reduce global carbon emissions by 14%.
Become an Essential Member of a Meaningful Team
These are the values that guide us toward success every day. If this sounds inviting to you, let’s meet.
A window into the future.
At Sustainix, we see a portal to what’s possible, and a new instrument to dramatically reduce emissions. We see the power to connect humankind with a greater vision. We see a new era where all people across the planet are living more sustainable lives. And we see a clear way to get there.
I am responsible for developing a long-term strategy to reduce the company’s environmental impacts across R&D, product development, energy, climate, water, materials and waste, and upstream and downstream supply chain. I enjoy this role because of the content and deliverables, both of which show how we care for our Earth, and we support the means to achieve an improved environment for our future generations. I also enjoy this role because of the people that I work with every day.”
Vice President, Sustainability
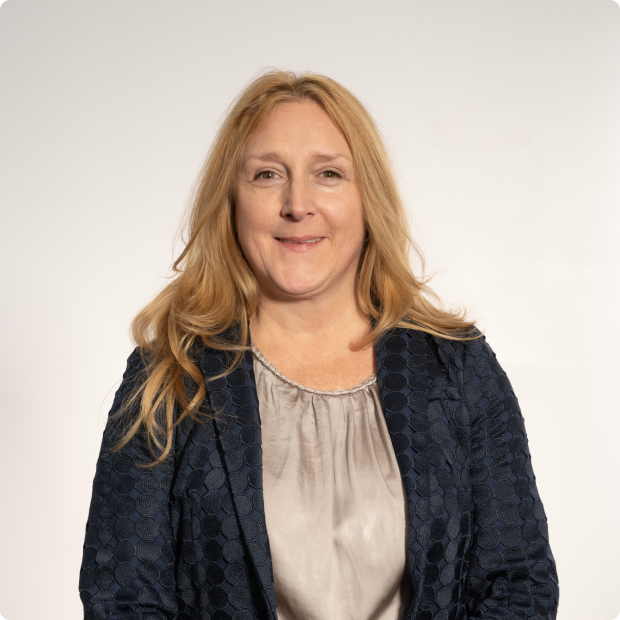
Career FAQs
After submitting your application, you will receive a confirmation email once Sustainix has received your application.
If your application meets our selection criteria, level of experience, and areas of expertise, our Talent Acquisition Manager will contact you for a prescreen interview to discuss your skills and experience via Microsoft Teams. If your skills and experience match the job requirements, you will be invited to participate in an onsite interview. Prior to the onsite interview, you will also be asked to complete a Personalysis; a personality assessment that helps Sustainix assess culture fit, communication style, and work preferences. During the onsite interview, you will meet with a team of individuals who understand the needs of the role. The onsite interview will last approximately up to eight hours. Sustainix will make a hiring decision after the onsite interview.
The prescreen interview is our chance to get to know you — from your education and skillset to your professional experience. It’s also your chance to ask questions and learn more about a career with Sustainix.
This is where we expand on the position you’re applying for and what’s expected of you to be successful in the role. We’ll cover the basics of the role, as well as where your skills and experience fit in and assess your company culture fit.
It is not recommended. During the application review, your skills and experience will be assessed for the best possible position fit.
Yes. We use a third-party administrator to perform a background screening as well as a 10-panel drug screening, which includes THC.
At Sustainix, we believe that collaboration is key to successful working relationships, and we feel the best way to do that is through an in-person, team-based environment. The majority of Sustainix roles require onsite work – lab-based R&D roles, product development, test and validation, and manufacturing.
Being a pioneer in sustainable technology, we are dedicated to cultivating inclusive and diverse teams. We view our people as our most valuable asset and aim for each individual to feel empowered to bring their authentic selves to work daily. Our objective is to foster a culture where everyone experiences pride and a sense of belonging. As a trailblazer in our field, we recognize the importance of creating opportunities for all to contribute to a cohesive and progressive workforce.
Sustainix is committed to ensuring we offer benefit plans and programs that improve your health, your family and your future. All employees are entitled to full medical, vision and dental benefits. Benefits are paid 80% company / 20% employee and are available to the employees on the first day of employment. Sustainix also offers a 401k program, paid time off (PTO), sick time off (STO), and numerous paid holidays.
Current Openings
LuxWall is focused on the product development, scaling and commercializing of innovative glass products and solutions for the built environment. LuxWall’s transparent insulation technology, Enthermal, provides a step change in energy performance by significantly reducing convective, conductive, and radiative heat gain and heat loss in buildings. Acting as a transparent thermos bottle for building, LuxWall has the potential to reduce global carbon emissions by more than 0.5 gigaton per year with mass adoption. Enthermal will forever change the way buildings are designed and constructed for the future sustainability of our planet.
The Warehouse and Packaging Associate will be responsible for the efficient operation of our warehouse facility. You will be responsible for various tasks related to receiving, storing, packaging, and shipping products ensuring accuracy, quality, and timely delivery.
Position Responsibilities
- Assemble and prepare products for shipment utilizing appropriate packaging materials based on product specifications and shipping requirements.
- Maintain efficiency of production to ensure timely assembly and shipment.
- Maintain proper storage of material and product inventory.
- Organize inventory in an easy-to-access process.
- Maintain the quality and upkeep of warehouse equipment including machinery, fixtures, and tools.
- Receive incoming shipment, inspect them for damages, and verify their accuracy against accompanying documentation.
- Sort, label, and store received goods in designated storage areas, ensuring proper organization and efficient space utilization.
- Operate warehouse equipment such as forklifts, pallet jacks, and hand trucks to move, stack, and transport materials, as necessary.
- Ensure the warehouse is clean and orderly.
- Collaborate with other team members to ensure smooth operations and customer satisfaction.
- Adhere to all company policies and procedures to maintain a safe working environment.
Position Requirements
- High school diploma or equivalent.
- The ability to operate a forklift is a plus but will train if needed.
- SAP experience, preferred.
- Exceptional attention-to-detail and a high sense of urgency.
- Ability to stand frequently, walk, kneel, and bend.
- Physical strength to manage demands such as lifting heavy objects.
- Effective communication skills, both verbal and written, to interact with team members, contractors, and employees.
- Ability to work independently and prioritize tasks in a fast-paced environment.
All applicants must complete and pass a drug screening and background check. LuxWall’s process is a 10-panel drug screen, which includes marijuana.
LuxWall is focused on the product development, scaling, and commercializing of innovative glass products and solutions for the built environment. LuxWall’s transparent insulation technology, Enthermal™, provides a step change in energy performance by significantly reducing convective, conductive, and radiative heat gain and heat loss in buildings. Acting as a transparent thermos bottle for buildings, LuxWall has the potential to reduce global carbon emissions by more than 0.5 gigaton per year with mass adoption. Enthermal™ will forever change the way buildings are designed and constructed for the future sustainability of our planet.
The Manufacturing Engineer is responsible for the process development, equipment development, process optimization, continuous improvement, process and equipment troubleshooting, and capital improvement projects related to the use of laser or thermal heating systems for processing advanced materials and products. The person must have the necessary knowledge and skills to support the LuxWall fail fast product development methodology with fast learning cycles for rapid commercialization. LuxWall is seeking a high-energy, entrepreneurial individual, laser or thermal process engineer who is looking for a manufacturing engineering challenge with growth opportunities.
Position Responsibilities
- Responsible for optimizing line flow, cycle time, uptime, and process yield through changes in tool programming, thermal heating or laser parameters, incoming material optimization, and incremental capital equipment for tool improvements.
- Maintain accurate and consistent schedules for projects and tasks for laser or thermal heat treatment engineering projects.
- Programming of laser or thermal in-line oven systems and related equipment as needed to support production needs.
- Help build preventative and predictive maintenance requirements and plans for laser or thermal processing-related equipment in manufacturing.
- Ensure the laser or thermal heating systems achieve critical targets, including output per hour, process yield, unscheduled downtime, MTTR, MTBF, number of required operators, and other critical parameters per manufacturing planning and targets.
- Work to help develop new laser or heat treatment systems for the plant to improve cycle times, quality detection/prevention systems, and uptime.
- Ensure that all equipment is installed and operated in a safe manner and has appropriate engineering controls, where applicable, to ensure safe operation.
- Develop written procedures for SOPs and work instructions for process operators and technicians with the metrics being defined as safety, quality, production outputs, and documentation.
- Collaborate with R&D organization for transfer of new products, processes, and equipment to high-volume production.
- Travel to multiple facilities as needed for completion of core job functions.
- Responsible for training process technicians on laser or thermal heat treatment and processing technology, tool operation, tool preventative maintenance, process metrology and quality control, and troubleshooting.
- Responsible for ensuring the laser or heat-treated materials, process, and equipment satisfy the cost of goods sold (COGS) targets, manufacturing cycle time, uptime, and yield and output per hour so the company reaches its COGS targets.
Position Requirements:
- Bachelor’s degree in mechanical or electrical engineering and minimum 5 years’ experience or engineering technology degree and minimum 10 years’ experience.
- A minimum of 2 years’ experience in lasers for welding dissimilar materials to rigid substrates or laser beam alignment, profiling, diagnosis, and characterization using laser power/energy meter, 2D/3D beam profilometer and photodiodes, is highly desirable.
- Successful completion of college or higher-level course (or equivalent projects) of thermodynamics, heat transfer, fluid mechanics, or laser, and those of materials science or material engineering.
- Knowledge of continuous convection, radiant, hybrid and millimeter microwave furnaces, or material characterization techniques for evaluation or laser processing of materials or components.
- Proven ability to apply statistical methods (DOE, SPC, etc.) to product development efforts.
- Good verbal and written communication skills.
- Excellent problem-solving, brainstorming, and troubleshooting skills.
- Highly proficient using MS Project software along with the MS Office product suite (Word, Excel, PowerPoint, Access).
- Extensive experience in formulating and managing project schedules using WBS and Gantt charts.
- Experience and exposure to working in high-volume manufacturing operations.
- Experience working with glass, coatings, fabricated glass, and glass system solutions is highly recommended.
All applicants must complete and pass a drug screening and background check. LuxWall’s process is a 10-panel drug screen, which includes marijuana.
LuxWall is focused on the product development, scaling, and commercializing of innovative glass products and solutions for the built environment. LuxWall’s transparent insulation technology, Enthermal™, provides a step change in energy performance by significantly reducing convective, conductive, and radiative heat gain and heat loss in buildings. Acting as a transparent thermos bottle for buildings, LuxWall has the potential to reduce global carbon emissions by more than 0.5 gigaton per year with mass adoption. Enthermal™ will forever change the way buildings are designed and constructed for the future sustainability of our planet.
The Automation Engineer performs system and tool level programming, new machine installation, tool upgrades and troubleshooting for various programs, industrial robotics, conveyor and product transfer systems, and manufacturing systems. This position will work with a large variety of equipment and technical systems, including, but not limited to: PLC systems, production robots, servo systems, HMI systems, and SCADA systems.
Position Responsibilities
- Develop, test, and deploy PLC programs, ensuring seamless automation and control of machinery and equipment across various industrial settings.
- Design intuitive human-machine interface (HMI) and supervisory control and data acquisition (SCADA) systems, empowering operators to efficiently monitor and manage industrial processes.
- Contribute to the design and development of hardware components, including sensors, actuators, and control systems, adhering to global industry standards and ensuring reliability and performance.
- Conduct rigorous testing and meticulous debugging of PLC programs and hardware systems, swiftly identifying and resolving issues to meet project deadlines and quality standards.
- Create and maintain comprehensive documentation of PLC programs, hardware designs, and system configurations, ensuring seamless knowledge transfer and streamlined project management.
- Collaborate with cross-functional teams to assist in the execution of automation and control projects, providing technical support during system installation, commissioning, and post-implementation phases.
- Stay abreast of the latest advancements in automation, PLC programming, hardware design, and related technologies, actively incorporating new knowledge into project solutions.
- Demonstrate a strong commitment to safety by integrating best practices in safety design and adhering to relevant safety regulations during the development and implementation of automation systems.
- Foster effective communication and cooperation with mechanical engineers, electrical engineers, and project managers to deliver cohesive and comprehensive automation solutions.
- Responsible for optimizing line flow, cycle time, uptime, and process yield through changes in tool programming, tool parameters, incoming material optimization, and incremental capital equipment for tool improvements.
- Maintain accurate and consistent schedules for projects and tasks for automation engineering projects.
- Help build preventative and predictive maintenance requirements and plans for automation-related equipment in manufacturing.
- Ensure programmed systems achieve critical targets, including output per hour, process yield, unscheduled downtime, MTTR, MTBF, number of required operators, and other critical parameters per manufacturing planning and targets.
- Ensure that all automation equipment is installed and operated in a safe manner and has appropriate engineering controls, where applicable, to ensure safe operation.
- Develop written procedures for SOPs and work instructions for process operators and technicians with the metrics being defined as safety, quality, production outputs, and documentation.
- Travel to multiple facilities as needed for completion of core job functions.
- Responsible for training process technicians on automation technology, tool operation, tool preventative maintenance, process metrology and quality control, and troubleshooting.
- Responsible for ensuring automation processes and equipment satisfy the cost of goods sold (COGS) targets, manufacturing cycle time, uptime, and yield and output per hour so the company reaches its COGS targets.
Position Requirements
- Bachelor’s degree in Electrical Engineering, Automation, Control Systems, or a related field.
- 3-5 years of experience programming and troubleshooting PLCs, robots, transfer systems, vision systems, material tracking systems, and high-volume manufacturing equipment.
- Demonstrated understanding of Ethernet cabling, addressing, and networking.
- Understanding of basic concepts of MMIs, familiar with PanelView Plus and PanelView hardware.
- Ability to design, diagnose, and troubleshoot vision applications.
- Demonstrated understanding of AC and DC motors and servo systems. Working knowledge of Kinetix and PowerFlex drives.
- Familiarity with PLC programming concepts (e.g., ladder logic, function block diagrams) and hands-on experience in HMI/SCADA development. Knowledge of hardware design principles and control systems is advantageous.
- Competence in at least one programming language (e.g., ladder logic, function block) is preferred.
- Strong problem-solving and analytical skills to identify and resolve challenges in automation systems effectively.
- Excellent verbal and written communication abilities to collaborate efficiently with team members and articulate ideas clearly.
- Capacity to multitask, prioritize, and adapt to changing project requirements and deadlines.
- Self-motivated and proactive approach to learning and taking ownership of tasks.
- A collaborative mindset and willingness to contribute ideas and support team goals.
- Advanced skill level with Microsoft Office Suite; Word, Excel, and PowerPoint.
- Ability to perform electrical troubleshooting and read electrical prints.
- Hands-on approach to problem solving and analysis.
All applicants must complete and pass a drug screening and background check. LuxWall’s process is a 10-panel drug screen, which includes marijuana.